徳島のスポーツジムの紹介
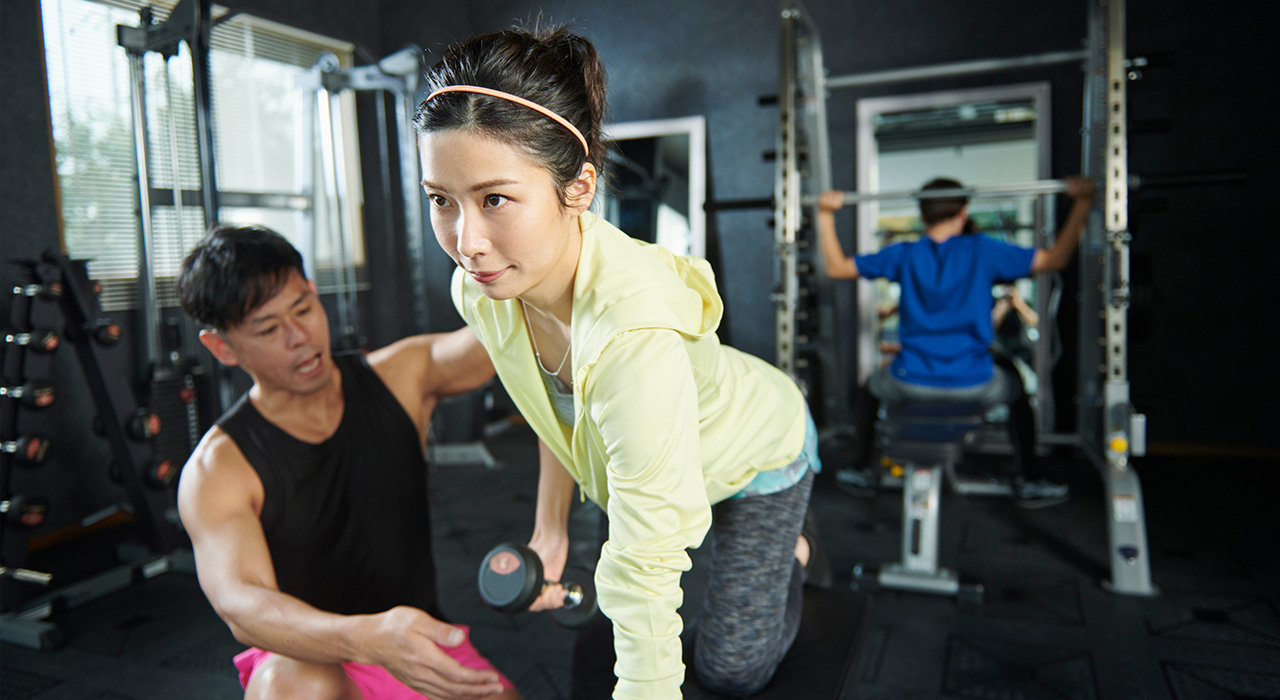
パーソナルトレーニングについて・トレーニングの目的とメリット パーソナルトレーニングは、それぞれの目標に合わせて行うフィットネストレーニングです。カウンセリングを通して、「やせる」「筋肉をつける」など、一定期間内で到達するための目標を設定し、マンツーマンで目標に邁進します。パーソナルトレーニングは、トータルで体作りを行うトレーニングです。 トレーニングジム パーソナルトレーニングの目的は、人それぞれさまざまです。元々、プロスポーツ選手が取り入れていたことから考えても、 「その人にとっての目的」 を実現するために、テーラーメイドのトレーニングを行うことがパーソナルトレーニングなのです。そのため、目的にもさまざまなものがあります。 ・体幹を鍛えるパーソナルトレーニング ・ダイエットを目的としたパーソナルトレーニング ・あたりの強さ(接触プレー)をつけるためのパーソナルトレーニング ・均整のとれたボディを作るためのパーソナルトレーニング など、それぞれに目的があり、その方法もさまざまです。